Is there hope for a sustainable future?
We are rapidly moving from an Oil Society to a Metal Society. Metals will be the centre and forefront of the entire sustainability journey. This is a quote from Staffan Lundgern Volvo Trucks Technology. It signifies the overall importance of metals as a foundation of a future sustainable society that provides a good quality life. It is not polymers, not wood, it is metals that will be our future!
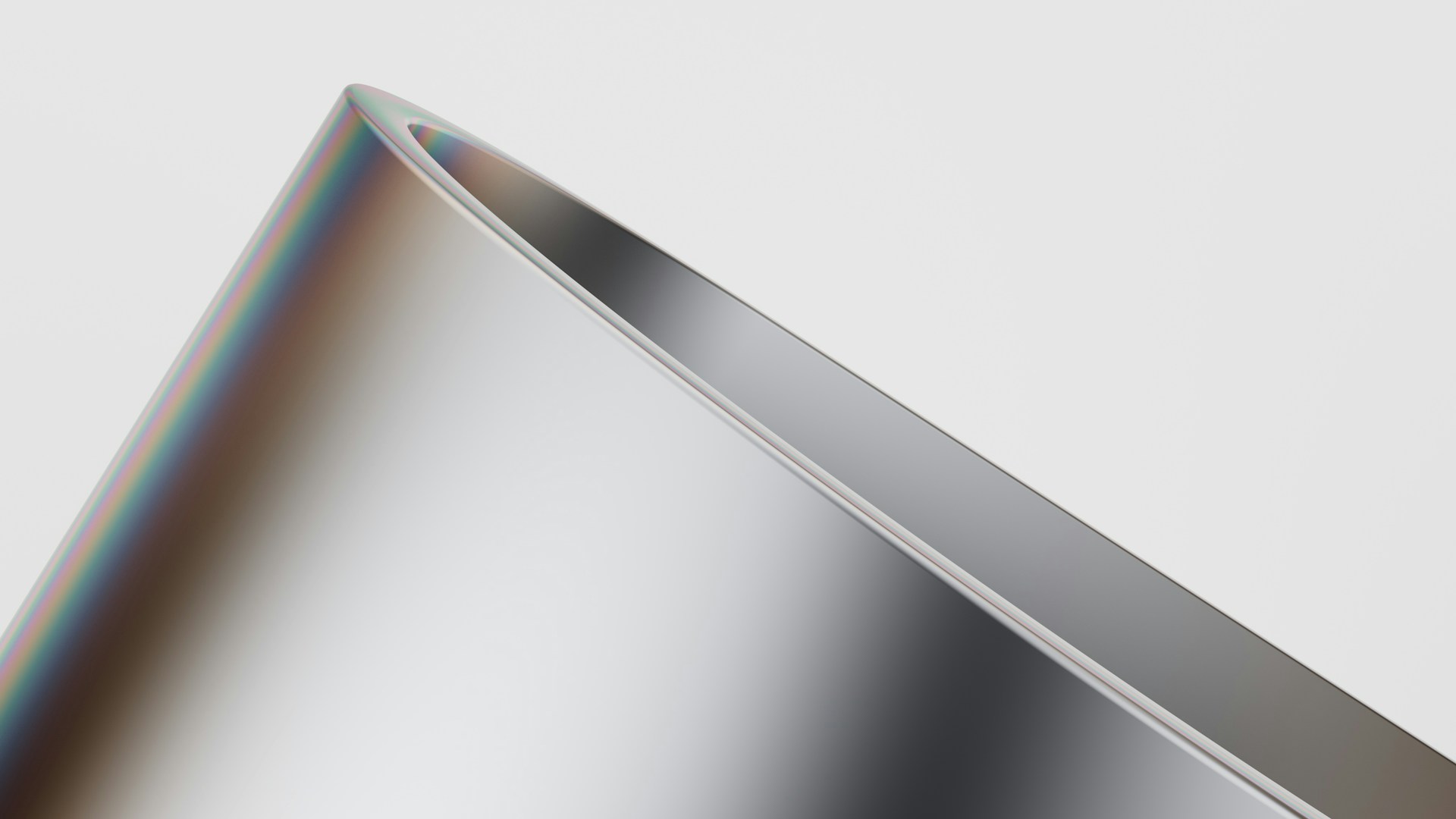
Photo by Max Zhdanov on Unsplash
The climate perspective
There is much discussion on sustainability, ranging from climate disasters to carbon dioxide and resource efficiency. In addition, sustainability is also related to wealth distribution, equality, security and freedom. This topic has many aspects, but understanding that global collaboration and joint economic growth are part of the solution is critical.
So what can we do? First, it is essential to understand that we can only do this together, and all need to do our part. For a metallurgist and a material such as aluminium and aluminium alloys, Staffan Lundgren, Volvo Truck Technology, said, " We are rapidly moving from an Oil Society to a Metal Society. Metals will be the centre and forefront of the entire sustainability journey". This statement gives me confidence that the work made by materials scientists is critical and vital.
What do we do?
One such effort is made in the project KlirAl, climate-adapted pure and recycled aluminium funded by Vinnova and Metallic Materials. This project is a collaboration between the research parts JU and Swerim supported by the Swedish aluminium industry and Stena Aluminium, Kubikenborg Aluminium, Gränges, Hydro, and Bryne. It has the foundation in that there are two main developments taking place. The first and most imminent is that recycling is critical to both the corbon footprint and the resource efficiency of aluminium components. There is an emerging research field popularly called SoDA or Science of Dirty Alloys. KlirAl primarily targets the cleaning of Fe and Cu as two difficult elements to manage in recycling. The second is more long-term, but significant progress is taking place in producing carbon dioxide-free primary aluminium. The leading cause of the carbon footprint of aluminium is the reduction of the aluminium oxide to aluminium where consumable graphite electrodes are used reacting with the oxygen in the aluminium oxide, forming carbon dioxide where three carbon dioxide atoms are formed for every four aluminium atoms. This is about to change! The problem is that the new pure aluminium is not so pure but contains high amounts of Fe. This is then something that should be dealt with. This is also a problem in common with recycled materials but with significantly lower amounts of other elements.
Where is the beef?
In the foundry industry, the formation of so-called sludge is a problem. Sludge particles are a relatively ill-defined compound but consist mainly of Al, Mn, Fe and Si. These particles can deliberately bind Fe to the particles by adding Mn and Si and controlling the temperature to form the sludge particles. These particles can then be separated. The KlirAl project targets this but focuses on making the formation more well controlled and well-defined so that the formed sludge particles can be more easily removed and the Fe content in the melt is minimised. What is important here is that the removed material becomes waste and can be made into a product. In the KlirAl project, there is a scale-up analysis activity to analyse and identify how a scale-up is possible together with the "productification" of the waste material
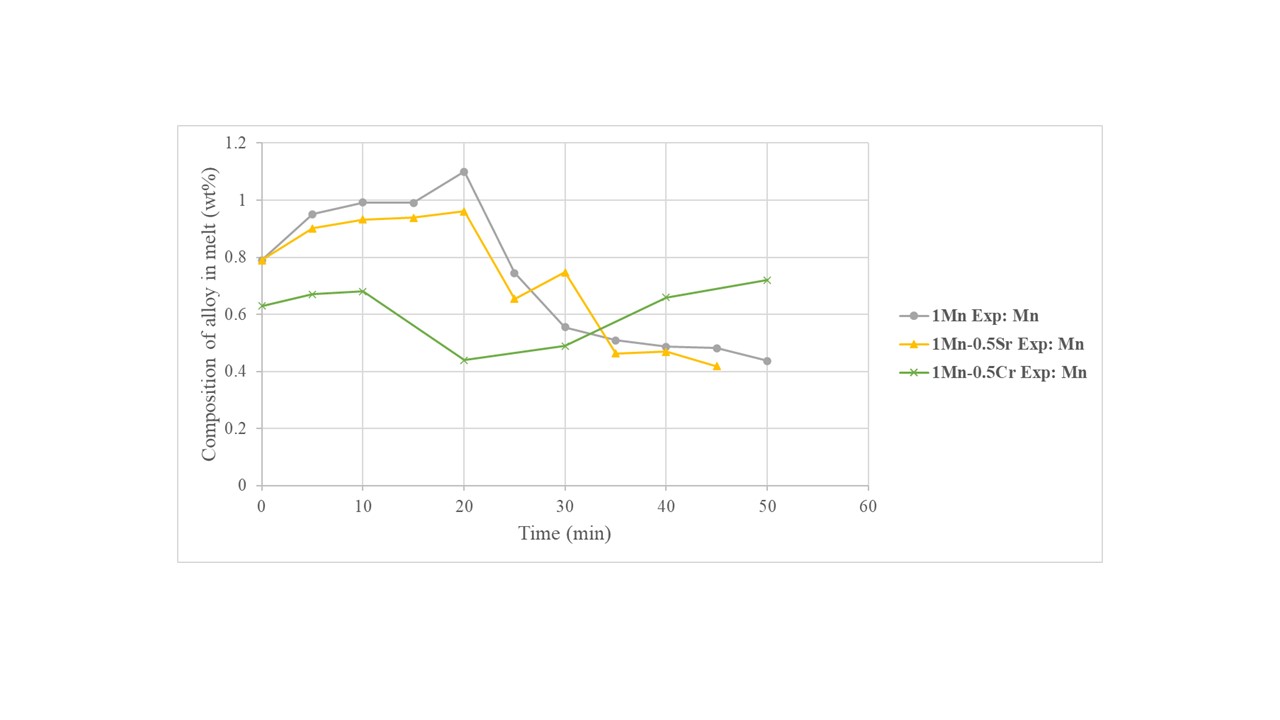
Figure showing the shange in concentration for different cleaning scenarios shong that reduction in composition can be difficult to achieve and requres further investigation
How about Cu, then? This is an entirely different matter as this will not readily form suitable particles in alloys with suitable compositions. As the temperature is reduced, it is enriched into the melt, and as the material solidifies, it ends up in the last solidified areas, together with Si, for instance. In the KlirAl project, a reasonably conventional approach is taken. This approach is called partial crystallisation. This means that temperature is reduced until a primary solid phase is formed, and the melt is enriched with the elements in the melt. There are several challenges here. The high-value material is the primary phase that is the purified material. The lower the temperature, the more this material is obtained and the better the process's yield. There is only one problem: the primary phase is as the melt is also getting slightly enriched with allying elements as the temperature is reduced, and there is a limit to how low you can go with a targeted composition for the purified material. The purified material in the KlirAl project aims to generate base alloys to allow the fabrication of 3xxx, 5xxx and 6xxx alloys important to the automotive and heat transfer industries. The remaining melt will be rich in many elements and most commonly resemble common cast materials. The challenge here is to maximise the value of the alloys produced, meaning that it is crucial to fit the composition of the primary phase to the wrought alloy to be made and maximise the wrought material yield. The tools in the KlirAl project involve working with alloy chemistry to control the solidification path and to develop an efficient extraction method for the secondary materials.
Detta är en bloggtext. Det är skribenten som står för åsikterna som förs fram i texten, inte Jönköping University.